Scale Smarter, Not Harder: How Operational Efficiency Drives Business Success
- David Mitchell
- Oct 12, 2024
- 3 min read
Updated: Oct 16, 2024
In today’s fast-paced business environment, operational efficiency is critical for staying competitive, scaling effectively, and ensuring long-term success. Companies that streamline their processes, minimize waste, and continuously improve their workflows are better positioned to adapt to market changes, meet customer demands, and achieve sustainable growth. At 3P Ventures, our Process Pillar focuses on helping businesses refine their operations to maximize efficiency, reduce costs, and enhance scalability.
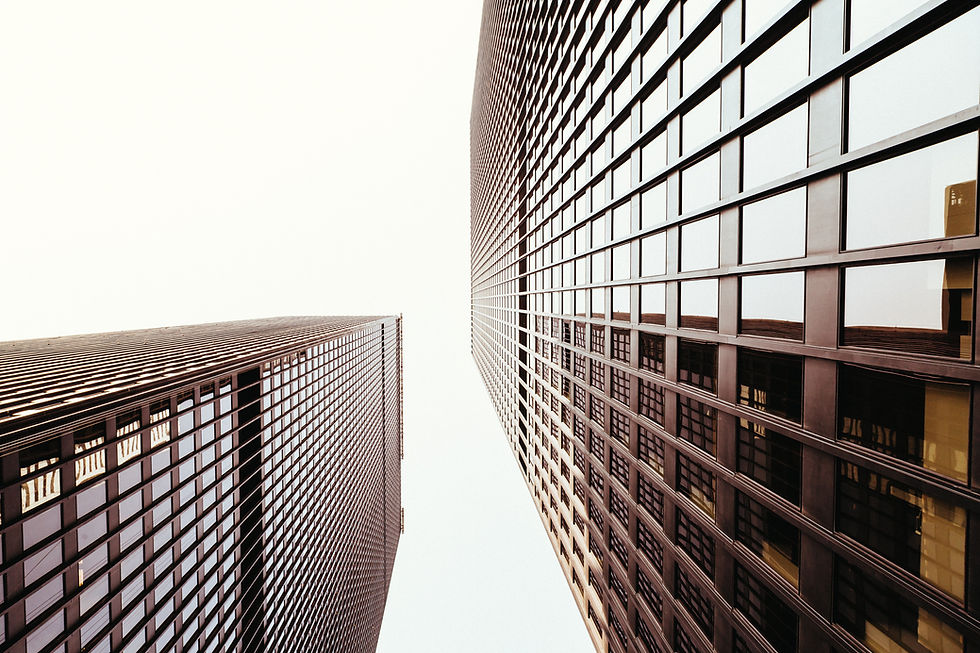
One of the most well-known examples of operational efficiency is Toyota, whose innovative approach to lean manufacturing and continuous improvement through the Kaizen philosophy has revolutionized industries across the globe.
The Toyota Case Study: A Masterclass in Operational Efficiency
After World War II, Toyota faced significant challenges, including resource constraints and the need to compete against larger automakers. The company needed a new approach to producing high-quality vehicles with fewer resources and less waste. This led to the development of the Toyota Production System (TPS), which introduced lean manufacturing principles. TPS focuses on minimizing waste, optimizing workflows, and creating a culture of continuous improvement through Kaizen (Toyota Motor Corporation, 2024).
Process Optimization Through Lean Manufacturing
Lean manufacturing principles were at the heart of Toyota’s transformation. By adopting the Just-In-Time (JIT) production method, Toyota reduced excess inventory and improved response times, producing only what was needed, when it was needed. This resulted in faster production times, lower costs, and greater flexibility (SSTLift, 2021).
Continuous Improvement (Kaizen)
The Kaizen philosophy, which translates to “continuous improvement,” encouraged all employees to contribute ideas for refining processes. This created a culture of ownership and engagement, leading to constant operational improvements (Leanscape, 2021). Kaizen remains a core principle of Toyota’s success, ensuring that processes evolve to meet changing demands.
Empowering People
Operational efficiency at Toyota wasn’t just about systems—it was also about empowering people. By encouraging employees to identify inefficiencies and propose solutions, Toyota created a deeply engaged workforce, invested in the company’s success. This people-first approach was essential to sustaining long-term efficiency gains (Xprrt, 2022).
Technology Integration
Toyota also embraced technology and automation where it added value. By integrating automation for repetitive tasks and maintaining human-driven processes for more complex activities, Toyota optimized both labor and technological innovation, ensuring efficiency without compromising product quality (SSTLift, 2021).
Results of Toyota’s Operational Efficiency Strategy
Toyota’s focus on operational efficiency delivered remarkable results:
• Reduced waste and costs through JIT and lean manufacturing principles.
• Faster production times, enabling Toyota to better meet market demand.
• Increased employee engagement, fostering a culture of ownership through Kaizen.
• Global leadership in the automobile industry, with Toyota becoming the world’s largest automaker by sales and production (Xprrt, 2022).
The 3P Ventures Process Pillar: Building Operational Excellence
At 3P Ventures, we draw inspiration from Toyota’s journey and apply similar principles to help our portfolio companies optimize operations and build scalable processes. Through our Process Pillar, we focus on:
1. Process Optimization: We identify inefficiencies, streamline workflows, and eliminate redundancies. Lean principles and task automation help businesses reduce waste and improve productivity.
2. Scalable Systems: We help companies implement scalable systems, whether through upgrading technology infrastructure, optimizing supply chains, or refining operational workflows.
3. Data-Driven Decision Making: We use key performance indicators (KPIs) to continuously improve operations. Data-driven decisions ensure long-term operational efficiency.
4. Employee Empowerment: Like Toyota’s Kaizen philosophy, we believe operational success is driven by people. We work with companies to empower employees to contribute to process improvements, creating engaged teams invested in their success.
Operational Efficiency: The Path to Long-Term Success
Operational efficiency is not just about reducing costs—it’s about building a foundation for sustainable growth. By focusing on efficient processes, companies can position themselves to scale, innovate, and remain competitive in a rapidly changing marketplace. At 3P Ventures, our Process Pillar ensures companies are equipped for long-term operational excellence, following Toyota’s lead in efficiency and scalability.
References
Leanscape. (2021). Optimizing efficiency: Inside the Toyota production system. Leanscape.io. https://leanscape.io/
SSTLift. (2021). Toyota’s lean management program explained. SSTLift. https://www.sstlift.com/toyotas-lean-management-program-explained/
Toyota Motor Corporation. (2024). Toyota production system: Vision and philosophy. Toyota Global. https://global.toyota/en/company/vision-and-philosophy/production-system/
Xprrt. (2022). Lean manufacturing at Toyota: A case study in manufacturing excellence. Xprrt Blog. https://blog.xprrt.com/lean-manufacturing-at-toyota-a-case-study-in-manufacturing-excellence/